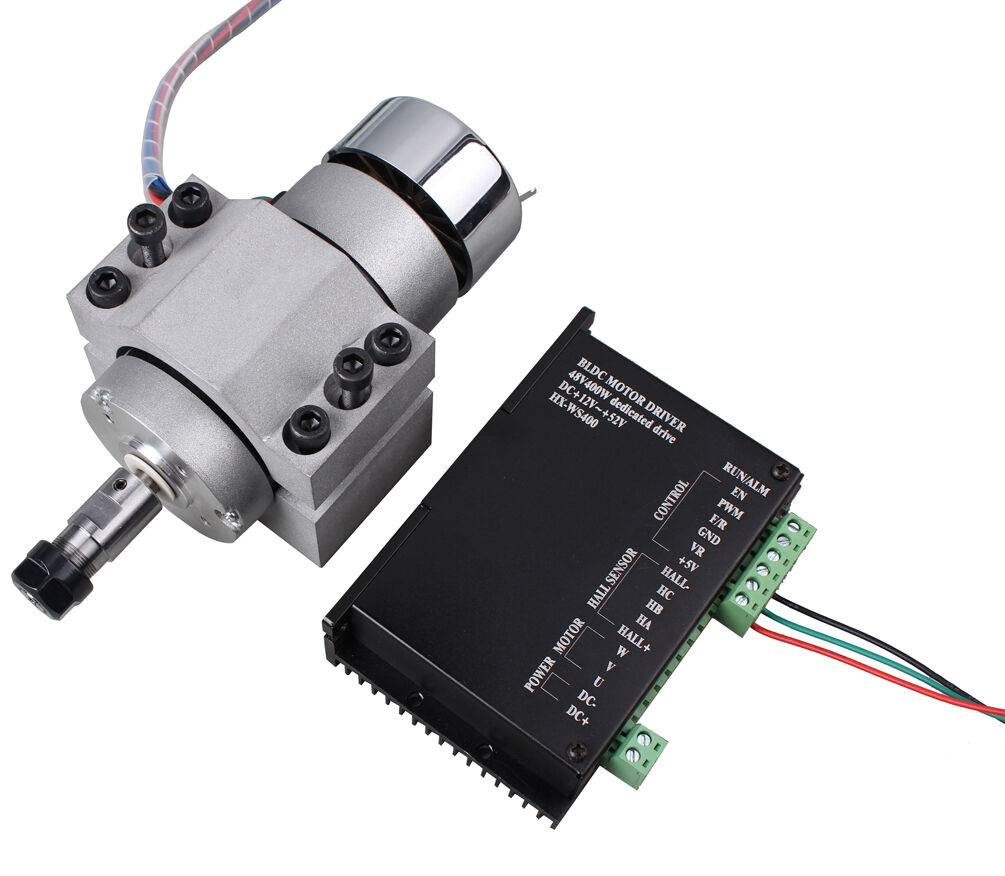
You see examples of BLDC motor controllers almost everywhere, but you may not know it. BLDC motor controllers use IGBTs (integrated-gate bipolar transistors) or FETs (field-effect transistors) to provide power to the motor’s coils. Many also use electronic commutation to drive coils, which switch the current between different phases.
When compared to their brush-type counterparts, BLDC motors are often considered superior. Here’s a look at the different components within their controllers:
Switch. This component breaks an electrical circuit, thus diverting or interrupting the current. The most common type of switch is an electromechanical device that you manually operate. Other kinds include biased (push-button), toggle (a rocking mechanism or a mechanical lever), rotary (like those in a multi-speed fan), knife, footswitch and reversing switches.
Relay. Relays operate the switch mechanism in BLDC motor controllers using electromagnets or other operating principles. Relays control circuits in controllers using a low-power signal.
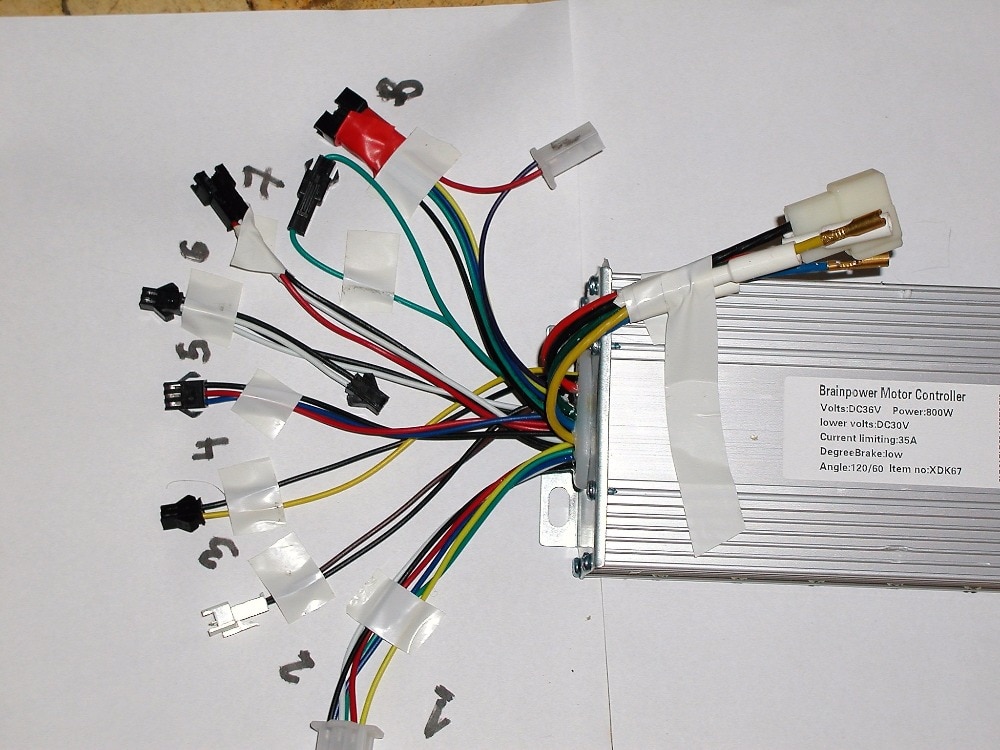
Contactor. Contactors are switches that are electrically controlled. They’re used for switching power circuits but have current ratings that are higher than those of relays. You may see a contactor in a magnetic starter.
Sensor. Also called detectors, sensors are converters that take measurements and convert the information into a signal that an individual or instrument can read. Examples of sensors include elevator buttons, speedometers, metal detectors, gas meters and altimeters.
Sensored and sensorless motors. These are the two main types of BLDC motors. In sensored motors, the controller determines the rotor’s position from the sensor signals. In sensorless motors, the controller measures the un-energized coils to the back EFM to determine the rotor’s position. Sensorless BLDC motor controllers don’t experience hysteresis, so they can quickly change directions.